งานไฟเบอร์กลาส...คืออะไร แบบไหนเรียกงานไฟเบอร์กลาส???
ปัจจุบันการทำชิ้นงานรูปแบบต่างๆ ด้วยไฟเบอร์กลาสนั้นขยายวงกว้างไปมาก เริ่มต้นจากโรงงานขนาดใหญ่ที่ผลิตจำนวนมากๆ เช่น บริษัท ทีเคดี จำกัด ผู้ผลิตกระบะต่อไฟเบอร์ยี่ห้อ แครี่บอยที่เรารู้จักกันดี, บริษัท พรีเมียร์ โพรดักท์ ผู้ผลิต ถังน้ำ พีพี ที่เราพบเห็นอยู่ตามบ้านทั่วไป หรือ บริษัท กระรัตที่ผลิตอ่างอาบน้ำ อคริลิค-ไฟเบอร์เป็นต้น
นอกจากนี้ยังมีผู้ผลิตรายใหญ่อีกหลายรายทำการผลิตชิ้นงานไฟเบอร์ออกมาขายในหลากหลายรูปแบบโดยที่ผู้ใช้อาจจะไม่ทราบว่า ผลิตภัณฑ์ที่ท่านใช้อยู่เป็นผลิตภัทฑ์ประเภทไฟเบอร์กลาสก็ได้ เช่น หลังคาแผ่นใส ท่อร้อยสายไฟ ถังเคมี รางน้ำ อุปกรณ์กีฬา เรือสำราญ หมวกกันน็อค และอืนๆ
เมื่อเวลาผ่านไปได้มีผู้ผลิตรายย่อยเกิดขึ้นอีกหลายรายทำการผลิตชิ้นงานรูปแบบต่างๆออกมาอีกมากมาย เราเริ่มเห็นอู่แต่งรถผลิตสปอย์เลอร์ และชุดสเกิ๊ต อยู่ทั่วไป ตามชานเมืองก็มีร้านขาย ผลิตภัณฑ์อื่นๆที่ทำจากไฟเบอร์กลาส เช่น เรือขนาดเล็กๆ ประมาณเเรือนากุ้ง เรือพ่นยาที่ใช้ในสวน จักรยานน้ำ รวมทั้ง ลูกหมุนระบายอากาศที่ใช้ติดหลังคาโรงงาน บ่อเลี้ยงปลา หินเทียม น้ำตกเทียม ไม้ท่อนเทียม แม้กระทั่งกังหันลมที่ติดอยู่ตามสนามกอฟล์หรือที่พักอาศัยก็ด้วย
ไม่เฉพาะชิ้นงานสำเร็จรูปเท่านั้นยังมีผู้ที่นำไฟเบอร์กลาสไปใช้ในงานซ่อมแซมต่างๆ เช่น เคลือบพี้นโรงงาน เคลือบดาดฟ้ากันน้ำรั่ว เคลือบถังเหล็กกันสนิมกันการกัดกร่อนของ กรด หรือ ด่าง เคลือบท่อโดยเฉพาะที่ต้องทนสารเคมีและอุณหภูมิสูงๆ แม้แต่ท่อน้ำทั่วๆไป ส่วนช่างซ่อมเรือ หรือกันชนรถยนต์นั้นใช้ไฟเบอร์กลาสกันมานานแล้ว
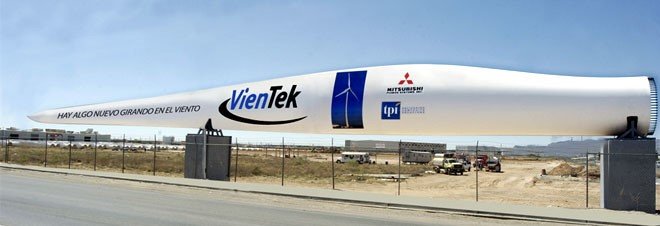
งานไฟเบอร์กลาส VS งานคาร์บอน
ก่อนที่อธิบายในกระบวนการทำงาน ขอกล่าวถึงความหมายของไฟเบอร์กลาสซักเล็กน้อยเพื่อป้องกันการสับสน กับเรื่อง เรซิ่น ใยแก้ว คอมโพสิท คาร์บอน และ เคฟลาร์ คือ ไฟเบอร์กลาสนั้นในเมืองไทยใช้เรียกชื่อชิ้นงานที่ขึ้นรูปด้วยเรซิ่นและใยแก้วเป็นส่วนประกอบหลัก
ส่วนชิ้นงานอื่นที่ขึ้นรูปด้วยเรซิ่น แต่ไม่ใช้ใยแก้ว เช่น ใช้เรซิ่นกับใยคาร์บอนก็จะเรียกคาร์บอนไฟเบอร์ ถ้าใช้เรซิ่นกับเคฟลาร์ก็จะเรียกว่าเคฟลาร์เฉยๆ แต่บางท่านเรียกคาร์บอนเป็นเคฟลาร์ก็มีเยอะ บางทีต้องถามกันให้ดีว่าหมายถึงตัวไหนกันแน่ ส่วนคอมโพสิทเป็นชื่อที่เรียกกว้างๆ ของชิ้นงานที่ทำขึ้นจาก เรซิ่น ผสมเส้นใยต่างๆ ไม่ว่าจะเป็นใยแก้ว ใยคาร์บอน ใยเคฟลาร์ หรือ ใยธรรมชาติ เช่น ใยปอ ใยสัปปะรด ก็แล้วแต่
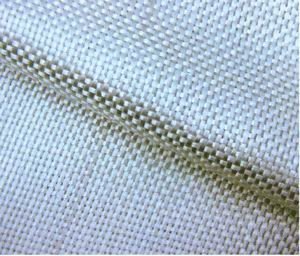 ผ้าทอใยแก้ว
| 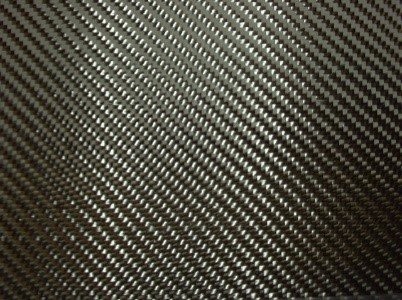 ผ้าทอใยคาร์บอน | 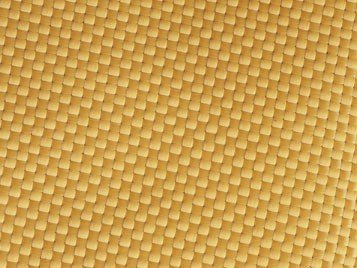 ผ้าทอใยเคฟล่า |
บางท่านอาจจะสงสัยว่าอะไรคือเรซิ่น?? อะไรคือใยแก้ว?? ก็ขออธิบายสั้นๆ ว่า เรซิ่น คือ พลาสติก ตระกูล โพลีเอสเตอร์ที่ไม่อิ่มตัว อยู่ในรูปของๆเหลวเหมือนยางไม้จึงเรียกว่าเรซิ่น พลาสติกชนิดนี้จะแข็งตัวด้วยการผสมสารเคมีอีกสองตัว (กรณีที่เป็นโพลีเอสเตอร์) ที่เรียกว่าตัวเร่งปฏิกิริยา และตัวช่วยเร่งปฏิกิริยา โดยตัวมันเองแล้วเรซิ่นเมื่อแข็งตัวจะมีความแข็งแรงอยู่พอสมควร สามารถทำเป็นชิ้นงานเล็กๆ โดยไม่ต้องผสมใยแก้วก็ได้ เช่นการหล่อตุ๊กตาหรือทำของชำร่วยต่างๆ แต่เมื่อนำมาทำเป็นชิ้นงานที่มีขนาดใหญ่ขึ้นและต้องรับน้ำหนักด้วยเช่น เก้าอี้ เรือ แผ่นหลังคา ก็จำเป็นจะต้องมีวัสดุที่จะเสริมความแข็งแรงเข้าไปในเนื้อเรซิ่น ดั่งเช่นการเสริมเหล็กเส้นเข้าไปในเนื้อปูน
ลักษณะของเรซิ่นจะมีความหนืดและสีเหมือนยาง
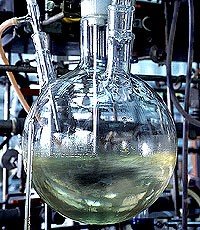
ในปัจจุบันวัสดุที่เข้ากันกับเรซิ่นได้ดี ที่มีราคาไม่สูงเกินไป และมีความแข็งแรงเพียงพอ ก็คือใยแก้วนั่นเอง ส่วนใยคาร์บอน และ ใยเคฟลาร์นั้น มีความแข็งแรงสูงกว่าแต่มีราคาสูงมาก จะใช้ในชิ้นงานที่ต้องการความแข็งแรงสูงๆ (และน้ำหนักเบาด้วย) เช่น อากาศ ยาน ยุทโธปกรณ์ และอุปกรณ์กีฬาเป็นหลัก ดังนั้นเราจะพูดถึงใยแก้วเป็นหลักในการทำชิ้นงานไฟเบอร์ใดๆ เมื่อกล่าวถึงใยแก้วแล้วก็ขอกล่าวเพิ่มเติมในที่มาของใยแก้วว่ามีที่มาเดียวกับแก้วน้ำที่เราใช้อยู่คือมีทรายเป็นส่วนประกอบหลัก แต่มีส่วนประกอบย่อยๆที่ต่างกันออกไปบ้างตามคุณสมบัติเรื่องความแข็งแรงที่ต้องการ ส่วนกระบวนการผลิตก็โดยการหลอมเหลวเหมือนกันแต่แตกต่างกันตอนการขึ้นรูปโดยการดึงให้เป็นเส้น แทนที่จะใช้การหล่อ หรือเป่าซึ่งเป็นกระบวนการขึ้นรูปภาชนะแก้วทั่วไป
กระบวนการผลิตชิ้นงานไฟเบอร์กลาสมีกี่รูปแบบ???
กระบวนการผลิตชิ้นงานไฟเบอร์กลาสนั้นมีหลากหลายรูปแบบ เช่นแบบใช้เครื่องพ่น เรซิ่นและใยแก้วไปบนแม่แบบ (โมลด์), แบบใช้ความดันหรือสุญญากาศในการดึงเรซิ่นเข้าไปในแม่แบบ หรือที่เรียกว่า แว็คคัม/อินฟิวชัน (ซึ่งเป็นแบบประกบ 2 ด้าน) หรือวิธีดั้งเดิมคือแบบใช้มือคนทาเรซิ่นลงบนใยแก้วที่อยู่ในโมลด์เลยก็ได้ซึ่งเป็นวิธีที่เราจะพูดถึงกันเพราะเป็นวิธีหลักที่ใช้กันอยู่กว่า 95% ของการผลิตชิ้นงานไฟเบอร์
กระบวนการขึ้นรูปชิ้นงานแบบ Hand Lay-Up
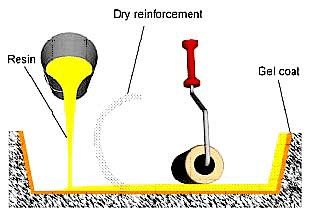
เริ่มที่ต้นแบบ (ปลั๊ก) เริ่มต้นของการผลิตชิ้นงานนั้นเราต้องมีต้นแบบหรือที่ภาษาช่างจะเรียกว่าปลั๊ก ซึ่งอาจเป็นการทำขึ้นมาเองเลยเช่นขึ้นโครงเรือที่ต้องการด้วยโครงไม้และไม้อัดตามรูปแบบที่วางไว้ หรืออาจจะใช้วิธีซื้อชิ้นงานสำเร็จรูปที่ราคาไม่สูงนักมาทำเป็นปลั๊กเช่นพวก สปอย์เลอร์ รถยนต์ก็ได้ การทำปลั๊กด้วยต้นเองนั้นแตกต่างกันไปในแต่ละความชำนาญและงานที่จะทำ บางท่านอาจถนัดที่จะขึ้นรูปด้วยพียูโฟม บางท่านอาจจะขึ้นรูปด้วยขี้ผึ้ง (โดยเฉพาะงานหล่อ) ก็ได้เหมือนกัน ปลั๊กนั้นเป็นจุดสำคัญของการผลิตชิ้นงานไฟเบอร์อย่างมาก เพราะถ้าปลั๊กทำออกมาได้ดี ขนาดและสัดส่วนถูกต้อง ผิวเรียบไม่เป็นคลื่น ขอบสันมุมไม่เบี้ยว โมลด์ที่ก๊อปมาจากปลั๊ก ก็จะดีตามไปด้วย และเมื่อนำโมลด์นั้นมาผลิตชิ้นงาน ชิ้นงานก็จะสวยงามและสัดส่วนถูกต้องใกล้เคียงกับปลั๊กมากที่สุด ถ้าผู้ผลิตชิ้นงานไฟเบอร์กลาสบางแห่งที่ยังไม่มีความชำนาญพออาจจะไม่ต้องการเสียเวลาหรือเสี่ยงกับการทำโมลด์เองก็อาจให้ผู้ผลิตรายอื่นที่มีความชำนาญมากกว่าช่วยทำโมลด์ให้ก็มี
2. การทำแม่แบบ (โมลด์) ก่อนจะเข้าสู่การทำโมลด์ขอให้ท่านผู้อ่านทำความเข้าใจของศัพท์ที่ใช้ในบทความนี้อีกสักครั้ง มีคำศัพท์อยู่สามคำที่จะใช้บ่อยๆสลับกันไปมาที่อาจทำให้เกิดความสับสนได้เวลาท่านผู้อ่านพบคำเหล่านี้ขอให้ใช้ความสังเกตด้วย
- ก. ต้นแบบ หรือเรียกอีกอย่างว่า ปลั๊ก หมายถึง ตัวเริ่มต้นที่เราต้องการให้งานออกมาเหมือนอย่างนั้น ยกตัวอย่างเช่น เราต้องการทำเรือ ด้วยไฟเบอร์กลาส โดยต้องการก๊อปจากเรือที่มีอยู่แล้ว ปลั๊กของเราก็คือเรือลำที่ต้องการก๊อปนั้น แต่ถ้าเราไม่ได้ต้องการก๊อปของใคร เราก็ต้องขึ้นรูปเรือขึ้นมาเองด้วยการทำโครงไม้อัดเป็นลักษณะลำเรือขึ้นมา โครงไม้อัดรูปเรือนั้นก็จะเป็นปลั๊กของเรา
- ข. แม่แบบ หรือเรียกอีกอย่างว่าโมลด์ เป็นตัวที่เราถอดแบบออกมาจากปลั๊ก โดยทั่วไปโมลด์จะทำขึ้นจากไฟเบอร์กลาส จะเป็นลักษณะกลับด้านกันกับตัวปลั๊ก โมลด์จะถูกใช้เป็นแม่พิมพ์ทำชิ้นงานออกมาได้เรื่อยๆ จนกว่าจะเสื่อมสภาพจึงจะต้องทำขึ้นมาให้มีความแข็งแรงทนทานเป็นพิเศษ
- ค. ชิ้นงาน คือผลิตภัณฑ์ไฟเบอร์กลาส ที่เราขึ้นรูปออกมาจากโมลด์ จะมีลักษณะกลับด้านกับโมลด์ นั่นก็คือจะมีรูปทรงกลับไปเหมือนกับปลั๊กที่เราต้องการก๊อปออกมานั่นเอง
กลับมาสู่การทำโมลด์ ซึ่งเราจะขึ้นรูปด้วยไฟเบอร์กลาสเพราะเป็นวัสดุที่เหมาะสมที่จะทำโมลด์ที่สุด มีในบางกรณีที่ผู้ผลิตใช้โมลด์เหล็กในกระบวนการผลิตแบบใช้แรงดันหรือสุญญากาศอัดเรซิ่นเข้าไปในโมลด์ที่เป็นแบบประกบ 2 ด้าน ส่วนกระบวนการผลิตแบบใช้มือทาเรซิ่นจะใช้โมลด์ด้านเดียวเท่านั้น ชิ้นงานที่ได้ก็จะเรียบแค่ด้านเดียวคือด้านที่สัมผัสกับโมลด์ ส่วนด้านที่ไม่สัมผัสกับโมลด์จะเห็นเป็นลายเส้นๆของใยแก้วอยู่
2. 1 เริ่มต้นการทำโมลด์จากการเตรียมวัสดุและอุปกรณ์ต่างๆดังนี้
1. เรซิ่นสำหรับทำงานไฟเบอร์กลาส
2.ใยแก้ว เบอร์ 300, 450 หรือ 600 แล้วแต่ความหนาที่ต้องการ
3.ใยทอ wr 400, 600, หรือ 800 แล้วแต่ความหนาที่ต้องการ
4.โมโนสไตรีน (โมโน) ใช้ผสมปรับความเหลวของเรซิ่นตามต้องการ
5.อาซีโทน ใช้ล้างเครื่องมือ
6.ตัวเร่งปฏิกิริยา (ตัวเร่ง) MEKP ใส่ให้เรซิ่นแข็งตัว
7.ตัวช่วยเร่งปฏิกิริยา (ตัวม่วง) โคบอลท์ ใส่ให้เรซิ่นแข็งตัว
8.ผงแคลเซียม ใส่เพื่อเพิ่มเนื้อ ลดต้นทุนการผลิต และให้เรซิ่นมีความแกร่ง
9.เจลโค้ท เป็นเรซิ่นที่มีความหนืดและความทนทานสูง ใช้เป็นผิวหน้าที่สัมผัสต้นแบบ
10.สีผสมเรซิ่น ใส่ในเจลโค๊ดให้มีสีในตัว
11.ขี้ผึ้งหรือน้ำยาถอดแบบ
12.ลูกกลิ้งใยสังเคราะห์สีขาว สำหรับทาเรซิ่นลงบนใยแก้ว
13.ลูกกลิ้งเหล็กสำหรับรีดน้ำยาและไล่ฟองอากาศ
14.อุปกรณ์เซฟตี้ในการทำงานเช่นผ้ากันเปื้อน ผ้าปิดจมูก ถุงมือ แว่นตา รองเท้าบู๊ท
15.อุปกรณ์อื่นๆ เช่น คัตเตอร์ หินเจียร์ กระป๋อง และขันสำหรับ ใส่ และตักเรซิ่น กระบวย สำหรับ ตวง MEKPหรือ ตัวม่วง (ห้ามใช้ร่วมกัน) กระดาษทราย ไล่เบอร์ 150, 320, 400, 600, 800, 1000 ถึงเบอร์ 1500 เครื่องขัดขนแกะ ขี้ผึ้งแดงขัดหยาบ ขี้ผึ้งขาวขัดละเอียด แว๊กซ์ขัดเงา ฯลฯ
2.2 เตรียมผิวปลั๊กให้สะอาดและเรียบเป็นมัน โดยการขัดแต่งให้สมบูรณ์ที่สุด ที่ต้องเตรียมผิวปลั๊กให้เรียบเงางามและสมบูรณ์นั้น เพื่อให้โมลด์ถอดออกมาจากปลั๊กตัวนั้นจะได้มีผิวเงางามและไม่ต้องเสียเวลามากในการแต่งซ่อมโมลด์ที่ไม่สมบูรณ์ นอกจากนี้ยังช่วยให้การถอดโมลด์ออกจากปลั๊กเป็นไปโดยง่ายด้วย
2.3 ขัดปลั๊ก 5 รอบสุดท้าย ด้วยขี้ผึ้งถอดแบบ ในแต่ละรอบให้ทิ้งเวลาห่างกันซัก 15 นาที ขี้ผึ้งถอดแบบนี้เป็นขี้ผึ้งที่ออกแบบมาเฉพาะสำหรับการถอดแบบชิ้นงานไฟเบอร์โดยเฉพาะ เนื่องจากเรซิ่นก็เหมือนกาวดีๆนี่เอง ถ้าเราไม่ลงขี้ผึ้งถอดแบบให้ดีก็อย่าหวังว่าจะถอดโมลด์ออกมาจากปลั๊กได้ ถึงออกมาได้ก็คงเสียหายทั้งปลั๊กและทั้งโมลด์แน่นอน
2.4 เตรียมเจลโค้ท ซึ่งเป็นเรซิ่นที่ใช้ทำชั้นผิวหน้าของโมลด์เพื่อให้ได้ความแข็งแกร่งของพื้นผิวและเป็นเงางาม ให้พร้อม
2.4.1 ถ้าเป็นเจลโค๊ทใสให้ใส่สีลงไปในอัตราส่วนที่ต้องการแต่ไม่เกิน 10% โดยทั่วไปสีที่เหมาะกับการทำโมลด์คือสีดำ หรือ น้ำเงิน บางท่านใช้สีแดง แต่ไม่ขอแนะนำเพราะบางทีสีแดงในโมลด์อาจตามไปที่ชิ้นงานที่ออกแบบมาให้เป็นสีขาวได้ ถ้าโมลด์เป็นสีดำหรือน้ำเงินถึงจะมีสีหลุดจากผิวโมลด์ตามไปบ้างก็ยังสังเกตยาก
2.4.2 ผสมตัวม่วงโคบอลท์ ลงในเจลโค๊ทในอัตราส่วนประมาณ 0.1% เช่นเจลโค๊ท 1 กก ให้ใส่โคบอลท์ แค่ 1กรัม เท่านั้น กวนส่วนผสมทั้งสองให้เข้าทั่วกัน
2.4.3 ใส่ตัวเร่ง MEKP ตามลงไปที่อัตราส่วนประมาณ 1% คือเจลโค้ท 1 กก ให้ใส่ตัวเร่ง 10 กรัม แล้วคนให้เข้ากัน โดยทั่วไปเมื่อผสมโคบอลท์ และ ตัวเร่งลงไปแล้วเรซิ่นหรือเจลโค๊ท จะเริ่มเป็นเจลจนทำงานไม่ได้ภายใน 20 นาที เพราะฉะนั้นการจะผสมเจลโค๊ทจะต้องผสมทีละน้อยเท่าปริมาณการใช้งานในแต่ละครั้งเท่านั้น มีข้อควรระวังคืออย่างใส่โคบอล์ทลงไปในตัวเร่งโดยตรงเพราะจะก่อให้เกิดปฏิกิริยาทางเคมีที่ให้ความร้อนสูงซึ่งอาจก่อให้เกิดอันตรายได้โดยง่าย
2.5 ใช้กาพ่นสีหรือเครื่องพ่นเจลโค๊ทพ่นลงไปบนปลั๊กที่เตรียมผิวไว้ โดยให้มีความหนาของเจลโค๊ทประมาณ .5มม-1 มม แล้วทิ้งไว้จนแห้งซึ่งก็จะใช้เวลาประมาณ 1 ชั่วโมง ในกรณีที่เป็นเจลโค๊ทผสมสีขาวหรือสีอื่นๆ แต่ถ้าเป็นเจลโค้ทผสมสีดำต้องรอให้แห้งนานกว่านั้น ถ้าไม่รอแห้งแล้วรีบลงชั้นใยแก้วและเรซิ่นต่อเลยจะทำให้เกิดรอยย่นขึ้นที่ผิวเจลโค๊ทเนื่องจากโมโนสไตรีนในเรซิ่นซึ่งมีอยู่มากกว่าจะไปละลายผิวเจลโค๊ทออก เจลโค๊ทที่เราพ่นลงไปบนปลั๊กนี้ก็คือผิวของโมลด์นั่นเอง
2.6 สัมผัสดูว่าเจลโค๊ทแข็งตัวแล้ว แต่ยังอาจนะเหนียวๆนิดหน่อยอยู่ก็ไม่เป็นไร ให้เริ่มเตรียมเรซิ่น(เกรดไฟเบอร์)ไว้ทำชั้นต่อๆไปของโมลด์ดังนี้
2.6.1 ผสมผงแคลเซียมลงในเรซิ่นเพื่อเพิ่มเนื้อตามต้องการ ซึ่งการผสมผงแคลเซียมนี้จะช่วยลดต้นทุนได้มากและช่วยเพิ่มความแข็งของพื้นผิว แต่ก็มีข้อเสียคือเรซิ่นจะเข้ากันกับใยแก้วได้น้อยลง, เรซิ่นแห้งช้าลง, เนื้อของโมลด์จะเสียความเหนียวแน่นไป ฉะนั้นผู้ผลิตชิ้นงานต้องดูถึงงานของแต่ละท่านเองด้วยว่าจะใส่ผงแคลเซียมมากหรือน้อยเท่าใด
2.6.2 ผสมโมโนสไตรีนเพื่อปรับลดความข้นเหนียวของเรซิ่นหลังจากผสมผงแคลเซียมไปแล้วเพราะผงแคลเซียมจะทำให้เรซิ่นมีความหนืดมากขึ้น
2.6.3 ผสมตัวม่วงโคบอลท์ ลงในเรซิ่นในอัตราส่วนประมาณ 0.1% เช่นเรซิ่น 1 กก ให้ใส่โคบอลท์ แค่ 1 กรัม เท่านั้น กวนส่วนผสมทั้งสองให้เข้ากัน
2.6.4 ใส่ตัวเร่ง MEKP ตามลงไปที่อัตราส่วนประมาณ 1% คือเรซิ่น 1 กก ให้ใส่ตัวเร่ง 10 กรัม แล้วคนให้เข้ากัน เช่นเดียวกับเจลโค๊ท เรซิ่นก็จะเริ่มเป็นเจลจนทำงานไม่ได้ภายใน 20 นาที เพราะฉะนั้นการจะผสมเรซิ่นจะต้องผสมทีละน้อยเท่าปริมาณการใช้งานในแต่ละครั้งเท่านั้น
2.7 เริ่มวางใยแก้วที่ตัดเตรียมไว้ล่วงหน้าตามรูปแบบของงานโดยวางใยแก้วลงไปแล้วทาเรซิ่นให้เปียกทั่วด้วยลูกกลิ้งใยสังเคราะห์แล้วรีดน้ำยาส่วนเกินรวมทั้งไล่ฟองอากาศออกด้วยลูกกลิ้งเหล็ก การวางใยแก้วแล้วทาเรซิ่นนั้นควรทำทีละชั้นเพื่อให้การทาเรซิ่น การรีดเรซิ่น และการไล่ฟองอากาศเป็นไปอย่างสมบูรณ์ทุกชั้น ทำทีละชั้นดังนี้จนได้ความหนาที่ออกแบบไว้ ถ้าต้องใช้ใยทอเพื่อเสริมความแข็งแรงของโมลด์ก็ให้ทำในลักษณะเดียวกันโดยถือเป็นชั้นหนึ่งของใยแก้ว อย่างไรก็ดีการรีดน้ำยาและไล่ฟองอากาศของใยทอนั้นจะเป็นไปได้ยากกว่าเนื่องจากความหนาที่มากกว่าและความหนาแน่นของเส้นใยที่มากกว่า
2.8 รอจนเรซิ่นแห้งสนิทซึ่งจะใช้เวลาประมาณ 3 วัน ถึงจะทำการแกะโมลด์นี้ออกจากปลั๊กได้ แต่ถ้าเป็นชิ้นงานขนาดเล็กก็จะใช้เวลาสั้นลง ไม่ควรรีบแกะโมลด์ที่ยังแห้งไม่ได้ที่เพราะโมลด์ที่ได้อาจบิดเบี้ยวพอนำไปขึ้นรูป ชิ้นงานที่ออกมาก็จะบิดเบี้ยวไปตามโมลด์เช่นกัน โดยทั่วไปนั้นผู้รู้ที่ออกแบบงานไฟเบอร์จะออกแบบมาให้การถอดโมลด์ออกจากปลั๊กและการถอดชิ้นงานออกจากโมลด์เป็นไปได้ง่ายที่สุดคือจะต้องไม่มีความลึกที่จะก่อให้เกิดสุญญากาศในระหว่างการถอด จะต้องไม่มีเหลี่ยมมุมที่ขัดขวางการถอด ผิวปลั๊กควรจะเนียนเรียบให้มากที่สุด ลวดลายต่างๆ ต้องไม่ไปขวางการถอดเป็นต้น ถ้ารูปทรงของปลั๊กซับซ้อนเกินไป ก็จะมีการแบ่งการทำโมลด์ออกเป็นส่วนๆแล้วค่อยมายึดประกอบกันด้วยน๊อตอีกทีให้เป็นรูปร่างโมลด์ที่สมบูรณ์อีกที ถึงกระนั้นก็ตามมักจะมีปัญหาการถอดโมลด์ออกจากปลั๊กไม่ออกอยู่เสมอ ซึ่งอาจจะมาจากแง่มุมใดแง่มุมหนี่งในการออกแบบหรือการเตรียมผิวปลั๊กตามที่กล่าวมาแล้วก็ได้ วิธีที่จะช่วยในการถอดคือใช้ค้อนยางเคาะจากด้านหลังของปลั๊กให้ผิวของปลั๊กกับผิวของโมลด์ที่ยังอาจติดอยู่ร่อนออก และเป็นการให้อากาศภายนอกเริ่มแทรกเข้าไปอยู่ระหว่างกลางของพื้นผิวทั้งสองได้ ถ้ายังไม่ออกให้เผยอขอบโมลด์แล้วใช้น้ำจากสายยางอัดเข้าไป บางท่านอาจจะใช้วิธีจุ่มทั้งปลั๊กและโมลด์ที่ไม่ใหญ่เกินไปนักลงในถังน้ำแล้วใช้น้ำจากสายยางอัดเข้าไปตามขอบที่เผยออยู่ น้ำในถังซึ่งมีความดันอยู่แล้วรวมกับความดันน้ำจากสายยางจะแทรกเข้าไประหว่างพื้นผิวทั้งสองแล้วช่วยให้การถอดโมลด์ออกจากปลั๊กได้ง่ายขึ้น ถ้ายังไม่ออกก็ต้องใช้วิธีเคาะฟังเสียงหาจุดที่ยังติดอยู่แล้วใช้ดอกสว่านเบอร์ 1/8นิ้วเจาะที่เนื้อโมลด์แล้วใช้เครื่องอัดอากาศอัดเข้าไปเพื่อให้อากาศไปแทรกระหว่างพื้นผิวของปลั๊กกับผิวโมลด์ที่ยังติดอยู่ให้ได้มากที่สุด เวลาเจาะให้หาตำแหน่งที่เจาะที่ท่านจะสามารถซ่อมโมลด์ได้ง่ายที่สุดด้วย
โมลด์ที่เราได้มานี้เป็นโมลด์ใหม่ที่ทางฝรั่งเรียกว่า Green Mold เป็นโมลด์ที่จะต้องมาทำความสะอาดและตกแต่งผิวที่อาจมีความเสียหายจากการถอดโมลด์อีกที โดยอาจต้องมีการโป้วแล้วขัดด้วยกระดาษทรายไล่เบอร์ไปจนเรียบเนียนแล้วขัดด้วยขี้ผึ้งขัดหยาบสีแดง ขัดละเอียดสีขาว ตามที่ได้อธิบายมาในขั้นตอนการเตรียมผิวปลั๊ก โมลด์ที่พร้อมใช้งานนั้นผิวจะเรียบเป็นมันเงาแต่ก็ยังมีความเสี่ยงว่าชิ้นงานอาจจะยังติดกับโมลด์ใหม่ได้เพราะในโมลด์ใหม่ยังมีโมโนสไตรีนที่ยังอยู่ในเนื้อเรซิ่นที่ยังระเหยไปไม่หมด จะค่อยๆออกมาซึ่งไอของโมโนสไตรีนจะสามารถทำลายชั้นขี้ผึ้งถอดแบบออกไปได้บางส่วนทำให้ถอดชิ้นงานออกจากโมลด์ใหม่ได้ยากกว่าโมลด์เก่าที่ใช้มาได้ซักระยะหนึ่ง
3. เริ่มต้นทำชิ้นงาน การทำชิ้นงานมีขั้นตอนที่คล้ายกับขั้นตอนการทำโมลด์มากคือเราจะก๊อปชิ้นงานออกมาจากโมลด์เหมือนกับที่เราก๊อปโมลด์ออกมาจากปลั๊กนั่นเอง แต่ต้องกล่าวซ้ำคร่าวๆบ้างเพื่อความสะดวกในการอ้างอิงเมื่อจะทำงานเป็นส่วนๆในอนาคต ขั้นตอนต่างๆมีดังนี้
3.1 เตรียมวัสดุและอุปกรณ์ตามหัวข้อ 2.1 เหมือนกับขั้นตอนการทำโมลด์ แต่อาจมีบางอย่างที่มากกว่าเช่นมีการใช้ ใยทิชชู่ ที่เป็นใยแก้วพิเศษ ใช้ทับชั้นสุดท้ายเพื่อช่วยปิดลายเส้นของใยแก้วให้ชิ้นงานดูเรียบร้อยขึ้น หรือการใช้ แผ่นเสริมความหนา ไม้อัด หรือแผ่นรังผึ้ง แผ่นเหล็ก ในการวางเสริมไปตามจุดต่างๆ ของชิ้นงานตามที่ออกแบบไว้ เพราะโดยทั่วไปชิ้นงานไฟเบอร์จะถูกประกอบเข้ากับชิ้นส่วนอื่นๆที่เป็นวัสดุต่างชนิดเช่นเหล็ก เช่นงานพนักเก้าอี้รถยนต์ เรือ อุปกรณ์กีฬา จะต้องมีการขันน๊อต ขันสกรูในจุดต่างๆ ก็ต้องฝังจุดยึดเหล่านี้เข้าไปในเนื้อไฟเบอร์ด้วย
3.2 เตรียมผิวโมลด์ให้สะอาดและเรียบเป็นมัน โดยการขัดแต่งให้สมบูรณ์ เพื่อให้โมลด์ที่ถอดออกมาจากปลั๊กตัวนั้นจะได้มีผิวเงางามและไม่ต้องเสียเวลามากในการแต่งซ่อมผิวชิ้นงานที่จะถอดออกจากโมลด์ตัวนั้น นอกจากนี้ยังช่วยให้การถอดโมลด์ออกจากปลั๊กเป็นไปโดยง่ายด้วย
3.3 ขัดโมลด์ 5 ครั้งสุดท้าย ด้วยขี้ผึ้งถอดแบบ ซึ่งเป็นขี้ผึ้งที่ออกแบบมาเฉพาะสำหรับการถอดแบบชิ้นงานไฟเบอร์โดยเฉพาะ ทุกครั้งที่มีการทำชิ้นงานจะต้องมีการขัดโมลด์ด้วยขี้ผึ้งถอดแบบนี้ เพราะขณะเมื่อถอดชิ้นงานออกจากโมลด์นั้นขี้ผึ้งที่ก่อตัวเป็นฟิลม์บางๆในตอนที่เราขัดจะหลุดติดไปกับชิ้นงานด้วย เมื่อจะทำชิ้นงานใหม่จึงต้องขัดโมลด์ด้วยขี้ผึ้งถอดแบบใหม่ทุกครั้ง แต่ผู้ผลิตบางรายก็จะลดจำนวนรอบในการขัดลงบ้างตามขนาดของชิ้นงานและความเก่า-ใหม่ของโมลด์
3.4 เตรียมเจลโค๊ทเพื่อใช้พ่นชั้นแรก โดยชั้นเจลโค๊ทที่พ่นไปบนโมลด์นี้ก็จะเป็นชั้นผิวหน้าของชิ้นงานเรานั่นเอง จะเป็นชั้นที่เราต้องการให้ชิ้นงานมีความเงางามและสามารถผสมสีเข้าไปในเนื้อเจลโค๊ทได้เลย ชิ้นงานที่ถอดออกมาจากโมลด์ก็จะเป็นชิ้นงานที่มีชั้นสีผิวหน้าอยู่ในตัว ไม่ต้องมาทำสีทีหลังอีก เราอาจจะข้ามชั้นเจลโค๊ทไปเลยก็ได้ถ้าชิ้นงานออกแบบมาไม่ต้องมีชั้นเนื้อสีเพราะเป็นชิ้นงานที่ต้องเอามาทำสีทีหลังอยู่แล้ว เช่นพวกชิ้นส่วนรถยนต์ หรือเป็นชิ้นงานที่ไม่ต้องการผิวที่เรียบหรือสวยงามมากนัก เช่นพวกถังน้ำ ถังเคมี แต่ถ้าเป็นชิ้นงานที่ต้องการโชว์ความสวยงามเช่นสปีดโบ๊ท เรือสำราญ เก้าอี้นั่ง แต่ไม่ต้องการมาพ่นสีทับให้เสียเวลา ชิ้นงานนั้นก็จะต้องมีชั้นเจลโค๊ทเป็นชั้นเนื้อสีด้วย
3.4.1 เริ่มต้นด้วยการใส่สีสำหรับทำงานไฟเบอร์ลงไปในเจลโค้ทในอัตราส่วนที่ต้องการแต่ไม่เกิน 10% ของปริมาณเจลโค้ท
3.4.2 ผสมตัวม่วงหรือเรียกอีกอย่างว่าโคบอลท์ ลงในเจลโค๊ทในอัตราส่วนประมาณ 0.1% ของปริมาณเจลโค้ท แล้วกวนส่วนผสมทั้งสองให้เข้าทั่วกัน
3.4.3 ใส่ตัวเร่ง MEKP ตามลงไปที่อัตราส่วนประมาณ 1% ของปริมาณ เจลโค๊ท แล้วกวนให้เข้ากัน โดยทั่วไปเมื่อผสมโคบอลท์ และ ตัวเร่งลงไปแล้วเจลโค๊ท จะเริ่มเป็นเจลจนทำงานอีกต่อไปไม่ได้ภายใน 20 นาที ย้ำข้อควรระวังอีกครั้งว่าอย่าผสมโคบอล์ทลงไปในตัวเร่งโดยตรงเพราะจะก่อให้เกิดปฏิกิริยาทางเคมีที่ให้ความร้อนสูงซึ่งอาจก่อให้เกิดอันตรายได้
3.5 ใช้กาพ่นสีหรือเครื่องพ่นเจลโค้ทโดยเฉพาะ พ่นเจลโค๊ทลงบนโมลด์ที่เตรียมผิวไว้แล้วโคยให้มีความหนาของเจลโค๊ทประมาณ .5มม -1 มม แล้วทิ้งไว้จนแห้งซึ่งปรกติจะใช้เวลาประมาณ 1 ชั่วโมง สำหรับเจลโค๊ทผสมสีที่ไม่ใช่สีดำ และใช้เวลานานกว่านั้น สำหรับเจลโค้ทผสมสีดำ
3.6 สัมผัสดูว่าเจลโค้ทแข็งตัวดีแล้ว ให้เริ่ม เตรียมเรซิ่นสำหรับทำชั้นต่อๆไปของชิ้นงานดังนี้
3.6.1 ผสมผงแคลเซียมลงในเรซิ่นเพื่อเพิ่มเนื้อตามต้องการ เพื่อช่วยลดต้นทุนและช่วยเพิ่มความแข็งของพื้นผิว โดยต้องระวังเรื่องเรซิ่นแห้งช้า และเนื้อของชิ้นงานจะสูญเสียความเหนียวแน่นไป รวมทั้งน้ำหนักของชิ้นงานก็จะเพิ่มขึ้นด้วย ผู้ผลิตบางรายอาจเปลี่ยนจากการใช้ผงแคลเซียมมาเป็นผงทัลคัมแทนเพราะไม่อยากให้ชิ้นงานมีน้ำหนักมากเกินไปเนื่องจากผงทัลคัมที่ปริมาณเท่ากันจะเบากว่าผงแคลเซียมนั่นเองแต่ก็มีราคาสูงกว่าด้วย
3.6.2 ผสมโมโนสไตรีนลงในเรซิ่นเพื่อปรับลดความหนืดเพราะผงแคลเซียมที่ผสมลงไปก่อนหน้านี้จะทำให้เรซิ่นมีความหนืดมากขึ้น
3.6.3 ผสมตัวม่วงโคบอลท์ลงไปในอัตราส่วนประมาณ 0.1 ของปริมาณเรซิ่นแล้วกวนให้เข้ากัน
3.6.4 ใส่ตัวเร่ง MEKP ตามลงไปที่อัตราส่วนประมาณ 1% ของปริมาณเรซิ่น แล้วกวนให้เข้ากัน เรซิ่นที่ผสมโคบอล์ทและตัวเร่งแล้วจะเริ่มเป็นเจลจนทำงานไม่ได้ภายใน 20 นาที
3.7 เริ่มวางใยแก้วที่ตัดเตรียมไว้ล่วงหน้าตามรูปแบบของงานโดยวางใยแก้วลงไปแล้วทาเรซิ่นให้เปียกทั่วด้วยลูกกลิ้งใยสังเคราะห์แล้วรีดน้ำยาส่วนเกินรวมทั้งไล่ฟองอากาศออกด้วยลูกกลิ้งเหล็ก การวางใยแก้วแล้วทาเรซิ่นนั้นควรทำทีละชั้นเพื่อให้การทาเรซิ่น การรีดเรซิ่น และการไล่ฟองอากาศเป็นไปอย่างสมบูรณ์ทุกชั้น ทำทีละชั้นดังนี้จนได้ความหนาที่ออกแบบไว้ ถ้าต้องใช้ใยทอเพื่อเสริมความแข็งแรงก็ให้ทำในลักษณะเดียวกันโดยถือเป็นชั้นหนึ่งของใยแก้ว
โดยทั่วไปการผลิตชิ้นงานมักใช้ชั้นใยแก้วน้อยกว่าการทำโมลด์เพราะไม่ต้องการให้มีความหนามากมายนัก ถ้าต้องการที่จะเสริมวัสดุอื่นเข้าไปในเนื้อชิ้นงานไฟเบอร์กลาสเพื่อให้มีความหนามากขึ้นเช่นไม้อัด ไม้บัลซ่า โฟม หรือแผ่นรังผึ้งตามการออกแบบที่วางไว้ในแต่ละส่วนก็วางลงไประหว่างชั้นใยแก้วได้เลย รวมทั้งส่วนประกอบที่จะใช้เป็นจุดยึดต่างๆก็วางสอดไปในขั้นตอนเดียวกับการวางชั้นใยแก้วเหมือนกัน ในกรณีที่ไม่อยากให้เห็นลายของใยแก้วโดยเฉพาะใยทอที่ด้านหลังของชิ้นงาน (ด้านที่ไม่ได้สัมผัสกับโมลด์) เด่นชัดนัก ก็จะใช้ใยผิวซึ่งเป็นใยแก้วชนิดหนึ่งแต่มีความเรียบเนียนและมีความบางมาก มาปิดทับแล้วทาเรซิ่นเป็นชั้นสุดท้ายได้
3.8 รอให้เรซิ่นแข็งตัวซึ่งระยะเวลาจะขึ้นอยู่กับปัจจัยเรื่องความชื้นในอากาศ อุณหภูมิ รวมไปถึงสัดส่วนในการใส่ โมโนสไตรีน ผงแคลเซียม และตัวเร่งด้วย เพราะผู้ผลิตบางท่านจะมีการดัดแปลงอัตราส่วนในการผสมเรซิ่นให้เป็นไปตามงานและสภาพอากาศในช่วงการผลิตชิ้นงานนั้นๆ แต่ปรกติแล้วผู้ผลิตมักรอให้เรซิ่นแข็งตัวไม่เกิน 2 ชั่วโมง ก็ถอดชิ้นงานออกจากโมลด์แล้ว ซึ่งบางกรณีที่รีบมากๆ แค่ 40 นาทีก็ถอดชิ้นงานออกมาแล้วมาให้แข็งตัวเต็มที่ๆนอกโมลด์อีกทีก็มี แต่สำหรับผู้ผลิตชิ้นงานขนาดใหญ่เช่น เรือสำราญมักจะรอกันถึง 2-3 วันค่อยถอดชิ้นงานออกจากโมลด์เลยทีเดียว ส่วนขั้นตอนการถอดชิ้นงานออกจากโมลด์ก็ไม่แตกต่างจากการถอดโมลด์ออกจากปลั๊กในขัวข้อ 2.8 นั่นเอง
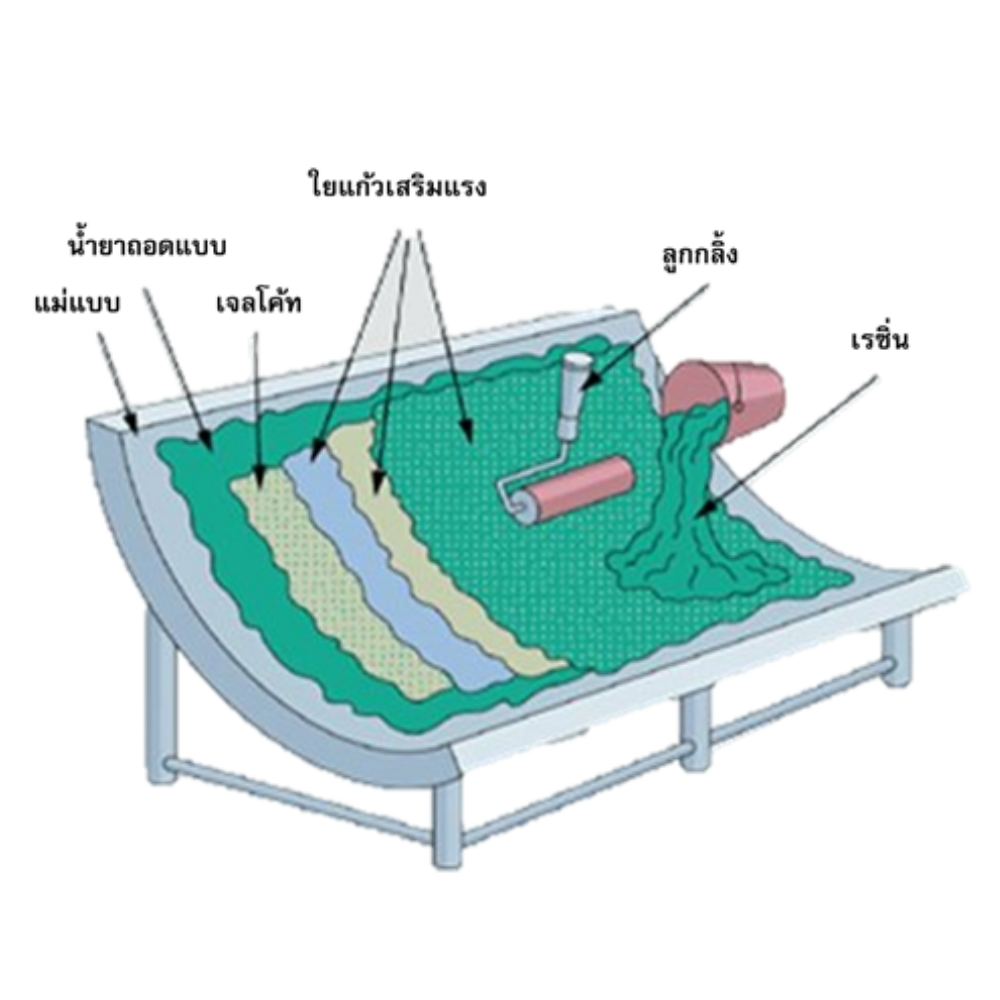